This section provides details of how to
construct a cluster of modules.
PD 600 series DPIs and I/O devices are
made up of two parts – the Terminal Base Module and the
Electronics Module.
Base modules are clipped directly onto
the DIN rail by holding at a slight angle while the front part is hooked
under the front edge of the rail, then pushed towards a horizontal position
until a retaining “click” is heard. They can be removed by pulling the red
spring-loaded slider outwards with a finger or small screwdriver, while
lifting the module away from the rail.
Electronic modules are simply plugged and
clipped into the appropriate base module, by first engaging the front
(optics) part of the electronics into the terminal module at a slight angle,
and then pushing towards a horizontal position until retained by the inbuilt
clip. Extraction is achieved by squeezing in the red retaining clip and
reversing the procedure.
Forming a cluster
Additional
base modules are fitted adjacent to one another, ensuring that the matching
retaining hooks are engaged, as illustrated. This ensures that the four Light-Link
communication windows in each module are correctly aligned.
|
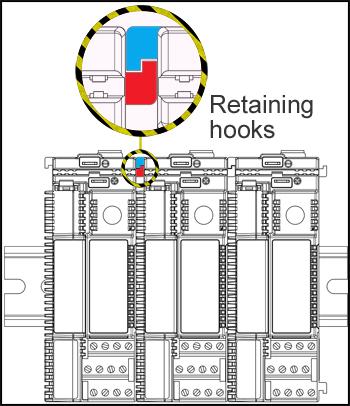
|
|
|
|
|
A cluster of distributed programmable
and input and output devices normally includes at least one device which
offers another P-NET interface in addition to Light-Link P-NET, to achieve
communication with the rest of the system. One way is to include a “Simple
P-NET Interface” module, which provides transparent RS485 P-NET communication
between the rest of the system and individual modules via Light-Link P-NET.
This configuration is especially suitable if no programmable control is to
be included within the cluster. On the other hand, if programmable control
is required, one or more DPI modules will be included, each of which offers
a choice of interface capable of communicating using the P-NET protocol. If
this method is used, the DPI will act as a gateway between the global P-NET
sectors and local devices connected to Light-Link P-NET.
|
|
|
|
|
Having assembled and applied any user
labelling to the cluster, it is now ready to have external connections
applied. Input and output terminations have been designed to ensure that no
additional junctions or marshalling connections are necessary. In other
words, there is a single terminal available for each wire (refer to terminal
labelling), and there is no need to common up any signals. As far as applying
power to each module in the cluster is concerned, this is simply achieved by
fitting (pushing in) the appropriate length of supplied double-sided Power
Rail, into the aligned rear slots along the length of the cluster. Connection
to the actual power source (which might also be fitted to the DIN rail), is
made using any two of the spade terminals available along the length of the
cluster. Under normal operational conditions, the cluster power rail will be
retained quite satisfactorily. However, under high vibration and/or mobile
conditions, retention can be guaranteed by passing a 2.5mm cable tie through
the hole formed between the rail and the electronics module and clip around
the engaged inter-module retaining spigots.
Light-Link is the means of communication
between 600 series modules. The common Tx and Rx optical paths are
automatically connected between terminal modules during placement, and an
optical “spur” connection is made available to any electronics modules that
are fitted. In copper wiring terms, using Light-Link is equivalent to
daisy-chaining a 3-wire connection between each module, but without having to
perform the time consuming and bulky physical connection. Such an optical
medium obviously provides galvanic isolation, but since light signals are
received, amplified and transmitted at each node junction (acting as a
repeater), this ensures optimal Light-Link signal anywhere in a cluster of modules,
no matter the number of modules.
It may
be more convenient to form a local cluster into two or more blocks, perhaps
in order to match with dimensions of a housing or
signal entry points. In this case, it is necessary to ensure that the
Light-Link communication path between modules is continuous. To achieve
this, two (or more) sub-clusters are linked together with two short pieces
of polymer optical fibre (POF). First, the plastic light guide assembly in
each of the linked terminal modules has to be removed. This can be achieved
by first removing any electronic module, and then using an ordinary paper
clip to push the guide out.
Note:
The POF cable type can be, for example,
Agilent Technologies type HFBR-RUS.
|
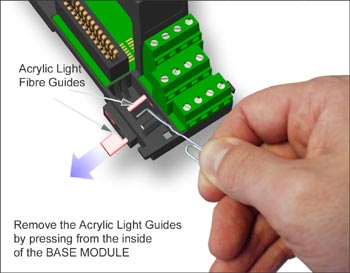
|
|
|
To ensure a clean interface, cut the
Polymer Optical Fibre (POF) to the length required, using the tool
illustrated below.
|
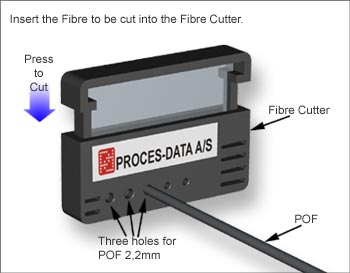
|
|
|
In joining clusters together, the
specifications provided below should not be exceeded.
Note;
|
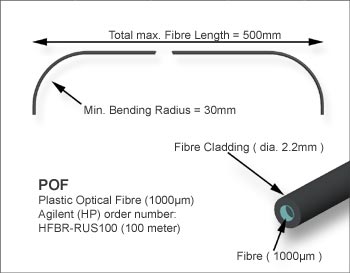
|
|
|
Next, the optical fibre is pushed into
the hole until it is in line with the edge of the hole inside the base
module. Now the electronics module is refitted.
|
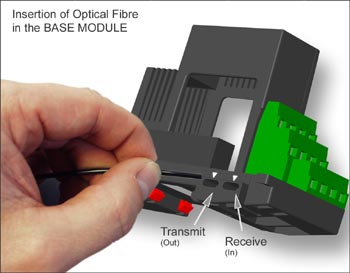
|
|
|
To ensure that the Optical Fibre is
retained under all operational conditions, a holding wedge can be fitted.
Note:
The holding wedges are delivered in
kits with short version wedges for left side mounting and long version
wedges for right side mounting. Always use the proper version, depending on
left or right side mounting.
|
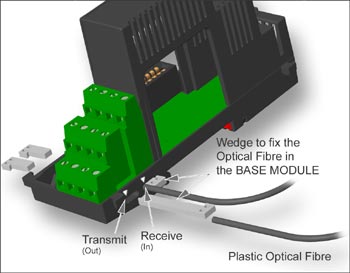
|
Power is linked between the
sub-clusters using the most convenient spade connections.
|
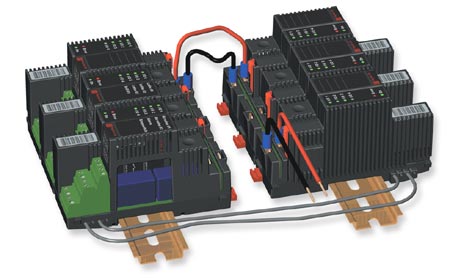
|
Related topics
Introduction to the PD 600 Series
Base module overview
|
|